Production technique [Setoguro]

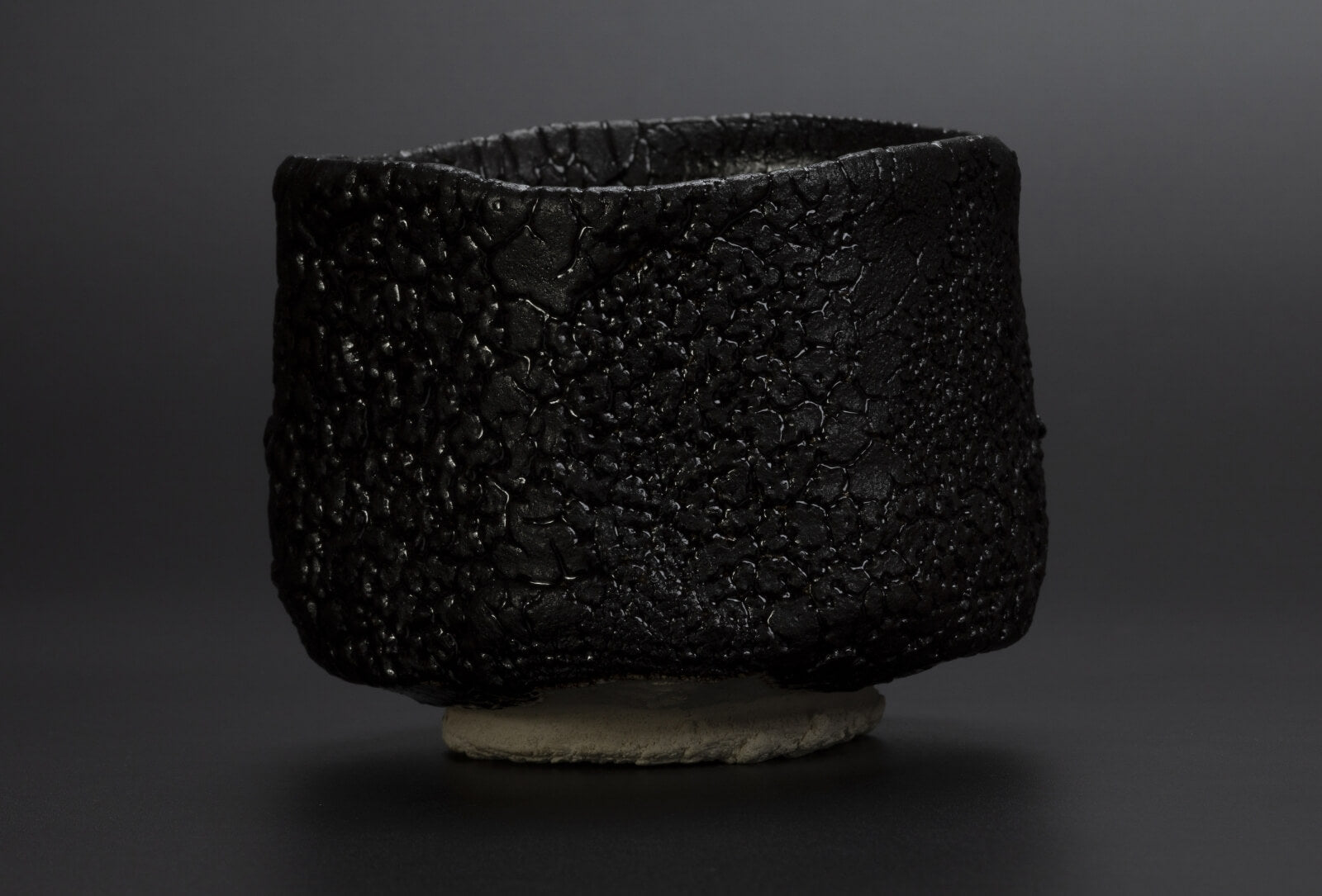
One from one kiln
Setoguro is characterized by its captivating black color.
To express this beautiful black color, a glaze mixed with ash is applied to oniita (clay containing iron) and fired at high temperatures. The technique involves removing it from the kiln while still hot and rapidly cooling it outside the kiln.
This is also known as "pulled-out black."
The phantom vessel "Setoguro," which was only produced for a mere 30 years in the world of tea over 500 years ago, is said to be a Japanese vessel with its own unique values within the aesthetic consciousness of wabi-sabi in the world of tea.
By pulling it out of the kiln at over 1,100 degrees and rapidly cooling it, it transforms into a beautiful jet black color while producing a beautiful sound (the sound of penetration).
Setoguro can only be fired up to three pieces in a single kiln firing.
It is extremely difficult to achieve a satisfactory black color, and it is considered good if a satisfactory piece can be produced from "one kiln to one piece."
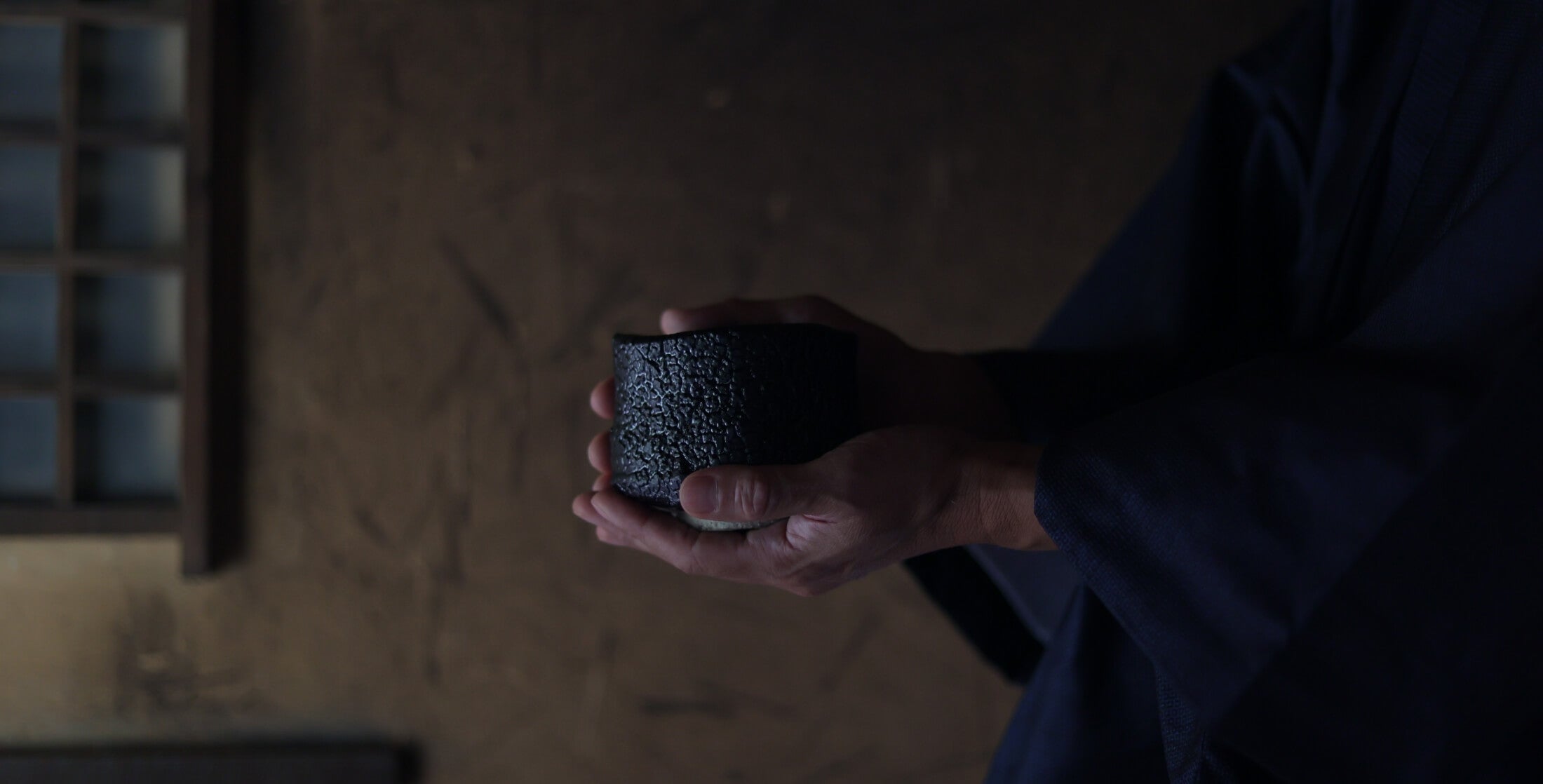
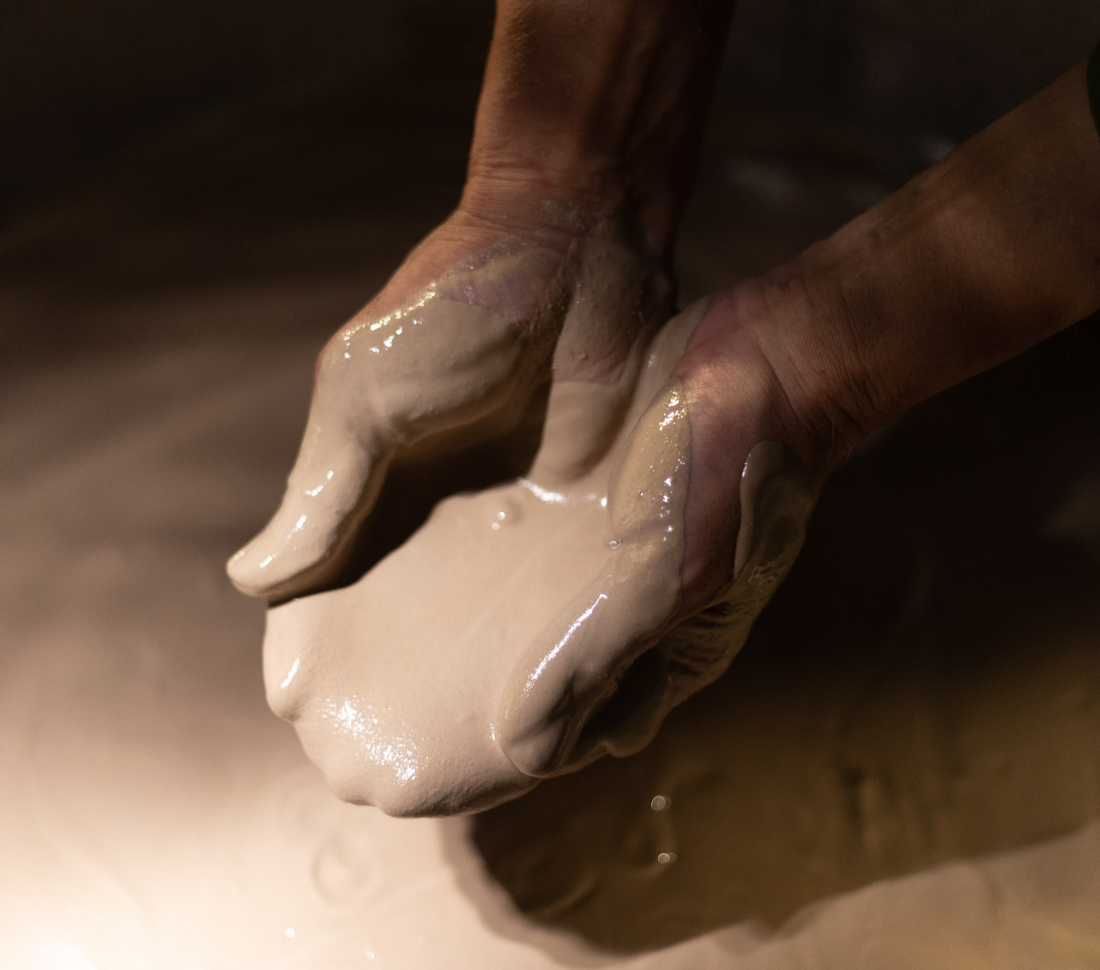
The raw material for Setoguro and Shino, Mogusa clay, is a rare clay that is difficult to obtain, destined to become the material for elusive vessels.
The clay found in the Mino region is considered rare even on a global scale.
Over thousands of years, volcanic activity and rain have altered its properties. The natural terrain, surrounded by mountains, has produced the unique clay specific to this region. The soil accumulated in this area, commonly known as Mogusa clay, contains a small amount of iron and can withstand rapid cooling. This results in the deep, absorbing black of Setoguro and the beautiful fiery red that symbolizes Shino. Mogusa clay is coarse and contains many fine air pockets, giving the finished product a warm and soft feel that fits comfortably in the hand.
100 days of pottery making process
The approximately 100-day pottery process until the completion of the vessel results in a unique creation born from various encounters and experiences.
Setoguro Matcha Bowl
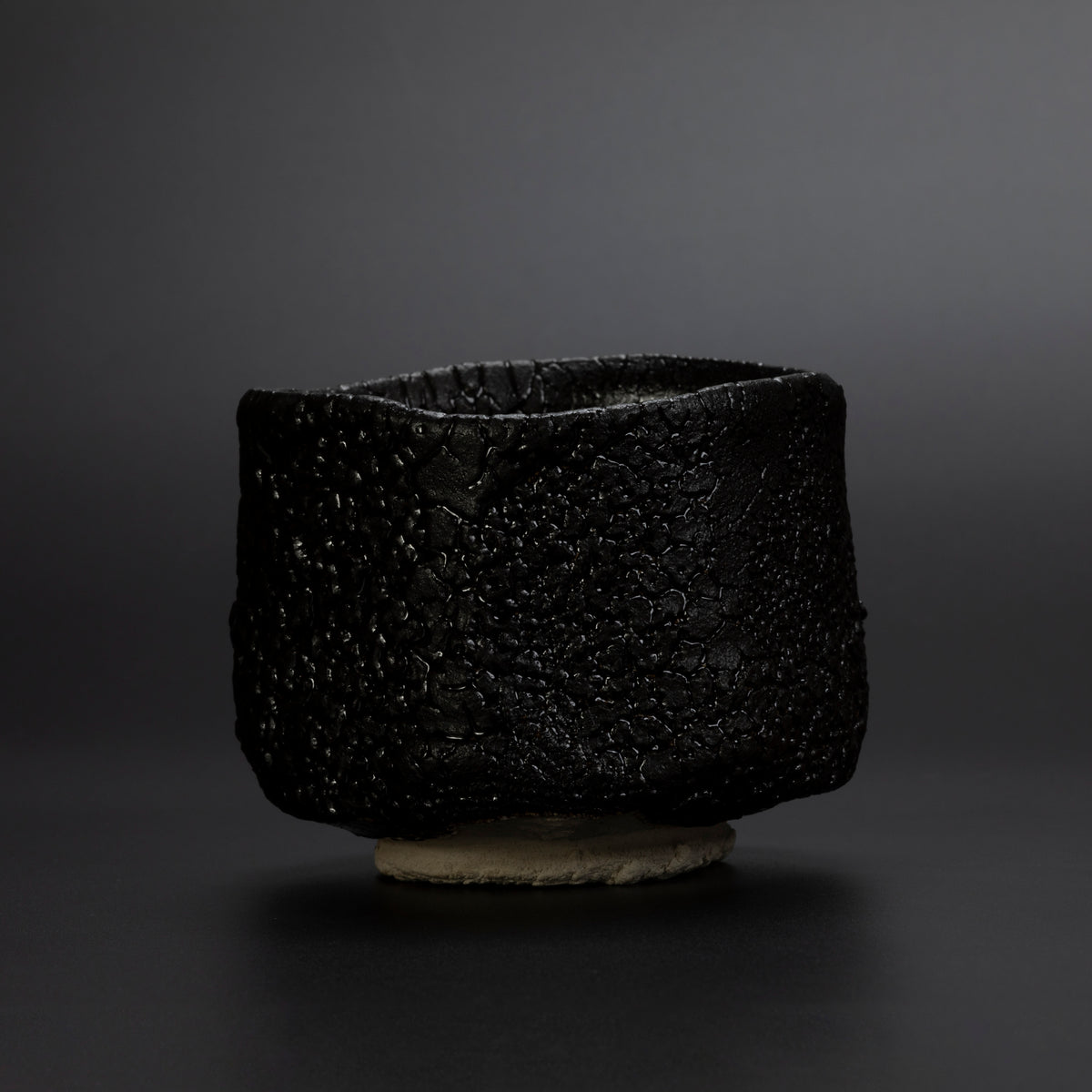
Setoguro Matcha Bowl
Setoguro is characterized by its captivating deep black color. Achieving this beautiful black involves applying a glaze made from Oniita (iron-rich clay) mixed with ash, and then firing it at high temperatures. While still hot, the piece is removed from the kiln and rapidly cooled—a technique known as "hikidashi-guro." Over 500 years ago, this elusive ware was produced for only about 30 years in the world of tea.
The Setoguro ware, which embodies the unique Japanese aesthetic principles of wabi-sabi, is known for its distinct value in the tea ceremony world. By pulling the piece from a kiln exceeding 1,100 degrees Celsius and rapidly cooling it, it transforms into a deep black while emitting beautiful sounds (crackling sounds) during the cooling process.
Due to the challenging nature of this technique, only up to three pieces can be fired in a single kiln at a time. Achieving a satisfactory black color is extremely difficult, and producing even one satisfactory piece from a single kiln firing is considered a success.
Setoguro plate

Setoguro plate
Five hundred years ago, black was considered a noble color.
Setoguro has a captivating, deep black hue that enhances the presentation of food on the plate.
How about using it for a special, vibrant main dish?
Enjoy a memorable time with excellent food, fine sake, and a superb vessel.
Additionally, as a decorative piece, a single Setoguro plate commands a strong presence, bringing an air of tranquility and gravity to any room.
Setoguro shunomi

Setoguro shunomi
For a solitary night of sipping sake, the Setoguro guinomi is ideal.
Setoguro is known for its captivating deep black color.
In the stillness of the night, lost in thought, why not enjoy a drink with a Setoguro guinomi?
Five hundred years ago, it was normal for rooms to be dimly lit even with lamps.
Today, turning on the lights can make a room as bright as day, but gazing at this vessel allows you to feel the depth of night from a time when electricity didn't exist, creating a perfect moment for contemplation.
In our current age overflowing with information, why not turn off the TV and smartphone, and simply gaze at the vessel, letting your thoughts wander?
How to use and care for your utensils
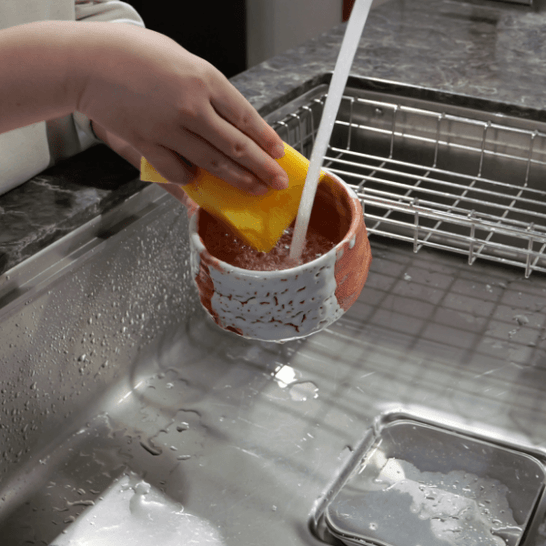
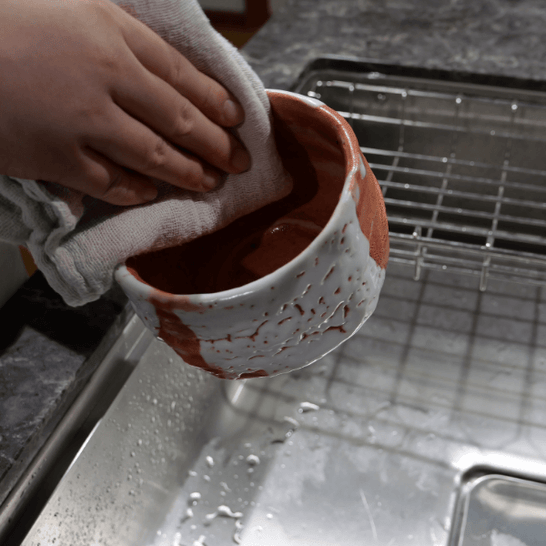
Wipe off the water with a soft cloth or kitchen paper.
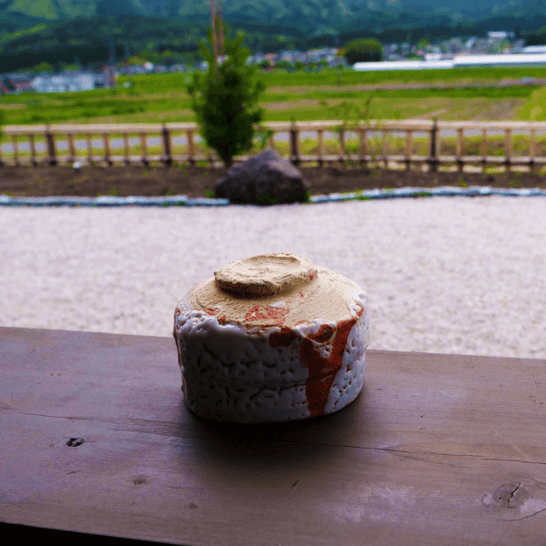
Sun-dry for 2 hours, or if the weather is bad or drying indoors, dry for 12 hours.
The bottom (foot) of the matcha bowl is where you can directly feel the rare clay, but it can absorb water.
To prevent mold, please complete the drying process as outlined in STEP 3.